风能利用开始于上个世纪70年代,而世界上第一个海上风电场,是1991年建成的丹麦温德比海上风电场,自此之后,海上风电得到快速发展。截止到2022年底,全球海上风电累计装机64.3GW,而中国海上风电的累计装机量为全球第一。中国海上风电的研究和探索开始于2000年左右,并在2010 年建成了亚洲首个大型海上风电场——东海大桥海上风电场。而到了2021 年,中国海上风电累计装机量27.68GW,同步实现了部分零部件如高端海缆、轴承等国产替代品。中国海上风电自起步至今,对于深远海的定义也有一个变化历程。最初的深远海定义为“双10”标准,即水深超过10米,离岸10公里。而目前行业公认的深远海为“双50”标准,即水深超过50米,离岸50公里。
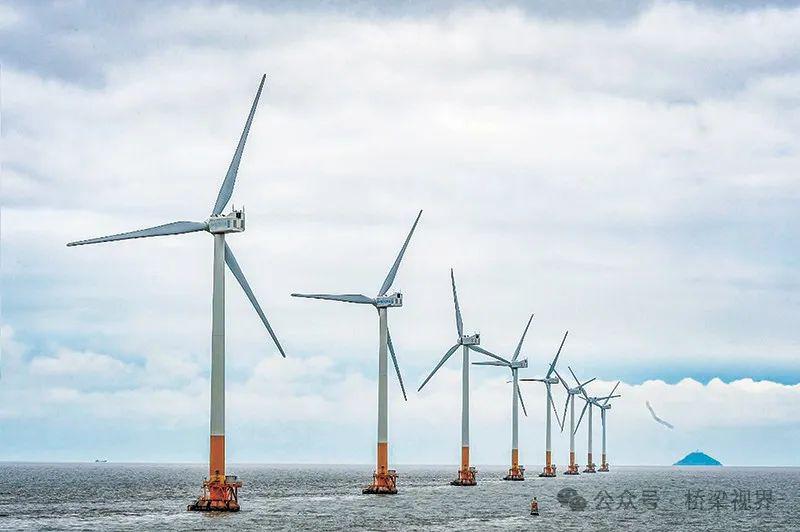
风能利用开始于上个世纪70年代,而世界上第一个海上风电场,是1991年建成的丹麦温德比海上风电场,自此之后,海上风电得到快速发展。截止到2022年底,全球海上风电累计装机64.3GW,而中国海上风电的累计装机量为全球第一。中国海上风电的研究和探索开始于2000年左右,并在2010 年建成了亚洲首个大型海上风电场——东海大桥海上风电场。而到了2021 年,中国海上风电累计装机量27.68GW,同步实现了部分零部件如高端海缆、轴承等国产替代品。中国海上风电自起步至今,对于深远海的定义也有一个变化历程。最初的深远海定义为“双10”标准,即水深超过10米,离岸10公里。而目前行业公认的深远海为“双50”标准,即水深超过50米,离岸50公里。

图1 2012-2022年中国海上风电新增和累计装机容量
中国风电&桥梁的独有特点
中国风电在走向深远海的过程中,逐步呈现出了自己的特点。
第一,基础结构多样化:海上风电的基础结构包含重力式、高桩平台、大直径单桩、吸力筒、导管架等结构形式,并开始了漂浮式风电的研究和实践。
第二,单机容量大型化:海上风电由最初的3兆瓦,逐步发展到现在的16兆瓦。
第三,安装工艺复杂化:截止到目前为止,中国海上风电已经形成了比较成熟的整体安装施工工艺和分体安装施工工艺;并结合深远海施工需求,开展了深远海大容量“运装一体式”海上风电机组安装技术的研究和实践。
第四,施工设备专业化:为了应对不同水深的施工作业,开发了适用于0-10米潮间带、可坐底施工的坐底施工船,建造大量的适用于70m以下水深的、自升式风电安装船;研制了适用于50m-100m水深复杂海况下,具备最新DP-2动力定位能力的海上风电作业施工船舶。

图2 中国海上风电施工工艺
中国的跨海大桥发展更为迅速,自20世纪80年代开始,我国已经先后修建海洋桥梁54座,无论是建设规模,还是工程影响都拥有着多项世界之最。包括:中国第一座外海跨海大桥——东海大桥,世界上最长的跨海大桥——港珠澳大桥,中国首座、世界最长的公铁两用跨海大桥——平潭海峡公铁大桥,世界上规模最大的跨海桥梁群-舟山连岛工程等。还有目前在建、世界最长、建设标准最高的高速铁路跨海大桥——杭州湾跨海铁路大桥,全长29.158km,其航道桥采用斜拉桥,主跨最大为450m,海中引桥为预应力混凝土连续梁,最大跨度80米,最大联长达3080米。

图3 东海大桥
面对复杂的海洋环境,跨海大桥具有工程规模大、施工难度高等特点,随着跨海大桥的发展,逐步呈现出了自己的特点。首先,随着港珠澳大桥等著名工程的修建,跨海大桥的离岸距离在不断增大。其次,海洋环境逐渐复杂,平潭海峡公铁两用桥施工中,局部区域7级以上大风超过200天,最大浪高近10米。第三,随着离岸距离逐步增大、施工水深逐渐增加、海洋地质环境越来越复杂。第四,基础规模越来越大,以港珠澳大桥为例,灌注桩平均长度130余米、直径2.5米,而平面偏差、倾斜度要求十分严格,施工难度逐步提升。
风电&桥梁深远海施工面临的风险挑战
随着海上风电和跨海大桥逐步走向深远海,面对复杂的海洋环境,海上施工会遇到一系列的风险和挑战。
因风浪环境多变性引发的船机设备风险。 深远海施工离岸距离远,风高浪大,对于施工作业而言,受波浪影响最大的是施工船舶。在实际施工过程中,因复杂的风浪环境而导致的施工船舶事故屡有发生,因此必须充分重视风浪对施工船舶安全的影响。
因地质条件复杂性引发的质量安全风险。 根据目前已有的施工经验可知,在距离海岸近70公里的海域,还存在深厚的淤泥层,在这种深水厚泥的环境下,进行1000吨到2500吨大直径钢管桩施工,施工难度大、质量风险高,深水、大浪、厚泥进一步加大质量控制的难度。
因基础结构深水化引发的施工安全风险。 海上风电最大单桩基直径10米多,长度最大能达到140米,重量2000多吨;而跨海桥梁的桩基多采用钻孔灌注桩,也有部分打入式钢管桩,两者单桩长度也多大于100米,施工过程中,“人、机、料、法、环”均面临巨大挑战。
因上部结构装配化引发的施工精度风险。 海上风机整体安装中,结构吊装高度为120m,重量约2000多吨,而对接安装平面精度需控制在2mm以内;同样,跨海桥梁施工,构件的体积和重量也日趋大型化,面临着船舶稳定性、吊钩定位、结构对中、构件碰撞、接头连接等系列挑战。

图4 风电&桥梁深远海施工复杂的风浪环境
综上所述,深远海施工对海上施工的船机设备、质量安全、施工风险、安装精度提出了新的挑战。
海上风电走向深远海的实践和风险控制
风浪环境多变性 对
船机设备 挑战的应对措施
海域风浪环境较恶劣,海上施工离岸距离远、施工窗口期短。因此,精准把握施工作业窗口和具有驾风驭浪的施工设备,对提升施工效率、保证施工进度、降低施工成本具有重要意义。在准确把握施工窗口期方面,应对措施:
开发了基于Web-GIS的海上风电施工作业窗口预报系统,对不同海域、不同船舶、不同工艺的作业窗口进行滚动预报,为现场施工提供及时数据支撑。该海上风电施工作业窗口预报系统,首次采用量化分析方法进行作业窗口预报计算,准确率90%以上;实现了施工全过程的自动计算、自动推送、滚动播报。同时,可以进行施工海域历史波浪数据查询、工程船舶选择、风场施工难度对比等功能。
开发驾风驭浪的施工设备——深远海固定式作业平台船的研发和应用。自升式平台船由上部结构(甲板)和桩腿组成,上部结构是一个驳船形浮体,可沿桩腿升降,工作水深为十几米到上百米。目前,海峰1001为国内首艘2500吨级第四代海上风电安装平台。海峰1002桩腿最长作业70m,甲板以上高160米,甲板面积达到了4500平,两艘船的抗风浪能力均达到了7级。为了应对更深水深的施工需求,建造了具备最新DP-2动力定位能力的、4000t全回转起重船、海峰2001,可进行100m水深复杂海况下的海上风电作业,结合运动补偿式抱桩器可进行15MW及以上大直径单桩基础等大型海上构件安装施工。

图5 基于Web-GIS的海上风电施工作业窗口预报系统

图6 海峰1002自升式平台船
地质条件复杂性施工
安全挑战的应对措施
十四五、十五五规划风场中,在离岸距离达到70km以上,依然有较为深厚的淤泥层,厚泥对于坐底式平台船、自升式平台船的影响较大。同时,深水厚泥、强硬岩基的地质环境,对于打入桩、嵌岩桩施工提出了新的要求。面对深远海复杂的地质环境,技术中心开展了“一机一算、一船一算、一桩一议”的技术支撑。应对措施:
针对坐底式平台船开展了船舶施工的力学过程相关基础性研究,建立了一整套船舶坐底作业分析方法。创造了浅层淤泥强度<10kPa的软黏土海床坐底施工的世界纪录。
针对自升式平台船开展了船体插拔腿施工与岩土介质力学过程量化分析,建立了一整套适用于我国软黏土海床地质的自升平台船站桩作业分析方法,站桩深度分析精确到1m,创造了桩腿入土36m深度的世界纪录。
针对打入桩开展了复杂地质条件下桩基可打性及入土深度量化分析,研究了大直径钢管桩打桩应力传播的三维效应,提出了桩身应力波波速简化计算公式及海利打桩公式参数取值的经验公式。建立了不同地质条件下打桩工程实测数据库。全面支撑了桩径9.3m、桩长107m、桩重1995t的桩基沉桩施工。

图7 自升式平台船插拔腿施工与岩土介质力学过程
基础结构深水化对
施工风险挑战的应对措施
随着海上风电施工的离岸距离越来越远,水深越来越深,海上风电结构的基础也越来越大型化,深水化。其中直径最大的单桩为10.4米、长112.米、重2407.5吨;吸力式导管架基础的吸力桶长40米、宽36米、高85米、重1936吨。基础结构深水化带来的运输、安装、打入、植入施工等难度大。 应对措施:
针对打入桩式大直径钢管桩开展了打入桩施工的整套核心技术及装备研究,基于单桩基础稳桩定位施工需求,创新研制了坐底式、桩船一体式、自升移动式、船载移动式等稳桩平台;实现了单桩桩长112.68米,最大桩径10.4米的打入施工。正在研制超大型液压打桩锤最大冲击能量5000kJ,最大能量打击频率18次/min以上,能够满足海上风电大直径8.5m以上桩基打桩需求。
针对大直径嵌岩桩开展了离岸无掩护和复杂地质条件下外海大直径嵌岩桩基础成套施工工艺;建立了稳桩嵌岩一体化平台搭设施工技术;提出了大直径嵌岩桩基础施工、质量控制措施;研发了深远海钻孔灌注桩无泥浆环保施工技术。在国内首次在140MPa极硬岩中,完成直径7.3m嵌岩桩基础施工。开发了破碎极硬岩石(100MPa~140 MPa)的反循环滚刀的大直径嵌岩钻机,该钻机可边钻进边扩孔,扩孔最大直径8.0m;设计了大直径单桩稳桩、沉桩、嵌岩一体化施工平台;研发了植入式大直径嵌岩桩基础灌浆全套技术及设备。
针对高桩承台结构形成了深远海高桩承台整套施工工艺及设备。其中,三航桩20具备最大桩径为5m、桩长105m+水深50m、桩重450t的作业能力;三航混凝土22可以实现两台泵每小时最多可生产混凝土250方,连续产量最高达2000方。系统化的全套施工设备可以实现深远海无平台高桩承台的无平台、快速施工。
针对桶式基础开展了深远海域海上风电桶式基础施工负压沉贯技术与装备研究,建立了基于土体强度指标和基于静力触探贯入阻力的两类桶式基础沉贯阻力计算方法之间的关系;研制了完全自主知识产权的负压桶沉贯施工成套专用设备与自动化控制系统,形成了一整套桶式基础负压沉贯施工工艺与高精度沉贯施工控制策略。

图8 离岸无掩护和复杂地质条件下外海大直径嵌岩桩基础成套施工
上部结构装配化
对安装精度挑战的应对措施
上部结构装配化带来的构件体积越来越大,吊装难度逐渐增加;结构更加复杂,对接精度要求增高;部分工程出现水下接头,连接材料的性能逐渐增强。 应对措施:
开展了大体积风机整体安装成套技术研究,开发了具有中国特色的风机整体吊装施工技术,单次吊装2000t;形成了一整套 “运装分离式”整体安装施工工艺,可实现滚动安装;创下了300台风机整体安装的纪录,是目前世界上整体安装施工经验最为丰富的施工单位。
针对安装精度控制开展了大型构件海上吊装精准对接控制技术,研发了吊钩GPS定位系统、自动对中执行机构、撞击加速度测试系统、加速度≤0.25g的柔性安装系统,同步精度、安装平面精度在2mm以内。开发了交互式风机整体安装模拟软件,实现了海上风机整体吊装过程人机交互、施工模拟和碰撞分级预警。
针对装配式构建连接问题,开展了海上风电导管架灌浆料及整体解决方案研究,该材料具有抗水分散性、大流动性、超高强、微膨胀、抗疲劳等特性。形成了专用的海上风电导管架灌浆施工设备、特殊的导管架水下灌浆施工工艺、导管架水下灌浆管路设计与灌浆封堵技术,导管架安装、调平、锁定与灌浆水下监控技术。

图9 大体积风机整体安装技术
跨海桥梁深远海施工的思考
随着跨海桥梁的逐渐发展,建设规模越来越大、离岸距离越来越远、海洋环境越来越复杂,结合海上风电的工程施工和技术研发,谈谈跨海桥梁深远海施工的思考。
针对风浪环境多变性的挑战,会导致跨海桥梁深远海施工面临作业窗口、船舶稳定性等问题。对此可以采用海上风电施工作业窗口预报系统,进行海上施工作业窗口精准预报;对于“深水大浪冲击性较强,临时工程难以施工”的区域,可采用自升式平台船或最新DP-2动力定位能力的船舶,进行50m-100m水深复杂海况下的施工作业。
针对地质条件复杂性的挑战,跨海桥梁施工也会面临钻孔灌注桩施工、打入式桩打入深度等问题,是否可用大直径钢管混凝土桩代替钻孔灌注桩,超大直径钢混桩可减少桩的数量,节省临时工程量,减少海上施工时间。目前,在深远海施工中已经可以实现最大桩径9.3m、桩长107m、桩重1995t的打入沉桩施工,以及在140MPa极硬岩中、直径7.3m嵌岩桩的施工,各类桩基有着完备的施工设备以及成熟的施工经验。
针对基础结构深水化的挑战,多样化的自升式平台船并自带1000-2400t全回转吊机,可以提供可移动、稳定、最大4000m2的海上作业施工平台,进行临时工程和下部基础的快速施工。同时,针对离岸距离比较远、水深特别大等不适宜搭建工作平台的区域,系列化钢管桩打桩船、运装一体施工船,混凝土搅拌船、自定位起重船,可以进行深远海高桩承台桩基的无平台快速施工,减少临时工程梁、节省施工工期和成本。
针对上部结构装配化的挑战,跨海桥梁施工也会面临深远海吊装难、水上对接精度及装配接头连接等问题。而最新DP-2动力定位能力、4000t起重船可以实现适应50m-100m水深复杂海况下常规构件的吊装。同时,大型构件海上吊装毫米级的精准对接控制、海上风电导管架灌浆料及水下灌浆整体解决方案等技术,也可以为吊装对接、接头连接提供很好的支持和服务。
走向深远海的工程建设,是时代发展的必然趋势。同时深远海的特殊环境也给我们提出了更大的挑战,深远海风电和桥梁施工尚面临着施工技术与装备双方面的升级需求,希望通过合作探索,让海上风电和跨海大桥进一步地走向深远海。