目前, 国内建设的大型焦炉主要有炭化室高7.63m 和7m 的顶装焦炉及炭化室高6.25m 的捣固焦炉。焦炉污染物排放分为两类,一类是装煤、出焦、熄焦时的阵发性排放,排放的粉尘量大,并与操作频度有关;另一类为不完全属于阵发性的有害气体。不同规格的焦炉,每天打开各泄漏口的次数及密封面长度不同,其排放的粉尘量和有害气体量也不同。采用大容积焦炉,生产同样规模的焦炭,由于每天打开泄漏口的次数少从而减少了污染物排放量。
目前,
国内建设的大型焦炉主要有炭化室高7.63m
和7m
的顶装焦炉及炭化室高6.25m
的捣固焦炉。焦炉污染物排放分为两类,一类是装煤、出焦、熄焦时的阵发性排放,排放的粉尘量大,并与操作频度有关;另一类为不完全属于阵发性的有害气体。不同规格的焦炉,每天打开各泄漏口的次数及密封面长度不同,其排放的粉尘量和有害气体量也不同。采用大容积焦炉,生产同样规模的焦炭,由于每天打开泄漏口的次数少从而减少了污染物排放量。
7m
焦炉的装煤除尘采用单集气管高压氨水喷射,上升管内形成一定负压,将装煤时的部分烟尘吸入集气管,另一部分烟尘经除尘装煤车,由地面站除尘风机抽吸至地面站进行除尘。为了提高装煤烟尘捕集效果,机侧推焦机上设有抽吸机侧炉门上方、平煤小炉门上方及炉门清扫装置上方逸散的尘的捕集净化装置。此外,推焦机上还设有平煤小炉门密封装置。
7.63m
焦炉采用PROven
系统配合除尘装煤车顺序装煤,装煤车装煤套筒设密封导套,装煤烟尘通过PROven
系统装煤时产生的负压由炉顶空间抽吸到荒煤气系统中。PROven
的核心是集气管负压操作,炭化室压力根据荒煤气发生量自动调节,使炭化室底部压力保持在40
~60Pa
,确保机、焦侧和炉顶区荒煤气不向大气逸散。其技术原理是在桥管末端设置1
根带槽口的皇冠管,伸入可以调节水位的固定杯中,根据从上升管采集到的压力来调节固定杯中的水位,相应调节皇冠管上的槽口开度值。
1)
装煤阶段的PROven
状态。氨水喷嘴喷洒氨水,冷却来自焦炉的荒煤气,大水量溢流管关闭后,液位调节阀动作,调节杯水出口完全打开。炭化室的荒煤气通过皇冠管末端的狭缝及调节杯下方的氨水出口进入集气管,以防止荒煤气外逸。装煤结束后,装煤车可以自动清扫装煤孔座,待装煤孔盖盖严后,对装煤孔盖与座之间的缝隙浇灌泥浆进行密封,防止装煤后烟气外逸。
2)
推焦阶段的PROven
状态。上升管水封盖完全打开,烧掉残余荒煤气及结焦期间产生的石墨。开启桥管内的氨水喷嘴,打开大水量溢流管,关闭液位调节阀,调节杯快速注水并溢流进入集气管。皇冠管的狭缝被水完全浸没,切断残余荒煤气在桥管与集气管之间的流通,防止空气进入集气管。
1)
大型捣固焦炉炉门高,开口面积大,装煤时机侧炉口长时间处于开放状态,故装煤烟尘排放难以控制,成为捣固焦炉大型化的主要制约因素。6.25m
捣固焦炉采用了将集气系统布置在焦侧,配合高低压氨水喷射装置、双U
形管导烟车、机侧炉门密封装置及炉头烟气抽吸装置,最大限度地控制烟尘的外逸。从投产后的效果看,集气系统布置在焦侧能更好、更快地将荒煤气导入集气管,环保效果良好。
推焦前和推焦杆退出后,特别是切煤饼机构工作时,机侧炉门外逸烟尘大,有时还有明火烧烤机侧拉条弹簧。机侧炉头烟气抽吸装置采用炉柱间的小集尘罩、集尘干管、中间车辆控制阀组合的抽吸方式,可解决烟尘外逸问题,避免烧烤拉条和弹簧,烟尘用抽吸装置直接送到出焦除尘管道,通过集尘管道到达出焦除尘地面站,无需增设其他设备。
捣固焦炉的双U
形管导烟车,采用了不同于其他捣固焦炉机械的工作方式。除尘导烟车在炉顶轨道上运行,车上布置了车体机侧U
型导烟管和车体中部U
型导烟管,构成双U
形管系统。上升管清扫装置、高低压氨水切换装置及上升管水封盖和阀体的启闭装置布置在车体的焦侧。
装煤推焦机上安装有活动的炉门密封框,在装煤过程中将煤饼和炉门框之间充分密封,导烟孔采用水封结构,U
型管通过导烟孔水封座与焦炉炭化室连通,提高了导烟孔的严密性。
装煤时可通过第(n+2
)孔桥管处高压氨水喷射产生的抽吸力,将正在装煤的第n
孔炭化室产生的烟气通过车体机侧的U
型导烟管导到第(n+2
)孔炭化室,进入集气管,防止炭化室机侧吸入空气直接进入集气管,也避免炭化室机侧有烟气逸出。随煤饼的装入,开启第(n
-1
)孔桥管处的高压氨水,借助其喷射产生的抽吸力,将第n
孔炭化室内产生的烟气经车体中部的U
型导烟管导人第(n
-1
)孔炭化室,进入集气管。随煤饼的继续装入,开启第n
孔桥管处的高压氨水,借助其喷射产生的抽吸力直接导入集气管。
2)
增设煤事故处理装置。捣固焦炉装煤掉角或塌饼时,会有大量煤粉散落在机侧操作台上,炉前余煤溜槽和余煤胶带运输机能快速将散落的煤料外运。捣固焦炉煤饼装炉时,可能出现煤饼未全部进入炭化室而无法安装机侧炉门的情况,捣固装煤推焦一体机安装了专用切煤饼机,可迅速切掉煤饼多余的部分,切下的煤料用炉前余煤溜槽和余煤胶带运输机快速外运。
煤事故处理装置主要由事故煤槽、煤槽下余煤胶带运输机、炉前余煤溜槽和余煤胶带运输机组成。事故煤槽在生产中用于煤饼实验,当生产不稳定时,通过实验来验证煤饼的稳定性,分析煤饼的倒塌原因。当装煤煤饼损坏而不能继续装入炭化室时,对事故煤饼进行处理。
除尘拦焦机采用两轨结构,集尘装置包括集尘罩及烟气外引机构,考虑到热浮力对烟尘收集的影响,焦侧增加了捕烟尘挡罩,以捕集摘焦侧炉门和推焦时从拦焦机烟尘罩和炉柱缝隙间泄漏的烟尘。在焦侧炉门打开前就位,抽吸炉门打开后炭化室正上方散发的烟尘及炉门处于清扫位置时散发的烟尘。
导焦栅两侧设置了挡尘板。导焦栅顶部及前端与炉框相接触部位的正上方及上部侧面位置设置了吸尘罩,以减小导焦时高温烟气受热浮力的影响,将出焦时的烟尘导入集尘干管中。除尘罩的后端与湿熄焦车上方主集尘罩进入除尘干管的管道相连,前端设置弹压式密封条,与炉柱正面接触加压密封。
出焦时采用定点接焦,其上方设置主集尘罩,收集出焦时的烟尘,并通过外引机构与除尘干管相连。主集尘罩由骨架和耐热不锈钢板组成,能适应热变形。烟气外引机构采用皮带小车,除尘干管布置在焦侧熄焦车轨道外的结构架上。
大容积焦炉的熄焦全部采用干熄法,干熄焦具有完善的除尘设施,除尘方式为地面站方式。湿法熄焦作为备用手段在干法熄焦检修时使用。针对湿法熄焦时约3m
的焦炭层厚度,设计采用稳定熄焦或压力熄焦技术,熄焦时间控制在90s
以内,焦炭水分稳定在3
%左右。熄焦塔上设有折流式粉尘捕集装置,用喷嘴对除尘片定期清扫,从而大幅降低吨焦粉尘的排放量。
大容积顶装和捣固焦炉采用的节能减排技术基本相同。7m
顶装焦炉装煤孔盖和捣固焦炉除炭孔盖采用球面密封,装煤孔盖与座间为球面接触,增加了装煤孔盖的严密性。
7.63m
焦炉的装煤孔座和孔盖的密封表面为圆锥形,密封性好。金属对金属的密封不能充分达到气密,使用泥封炉盖,其操作由装煤车自动控制,装煤孔座可使装煤车套筒、装煤孔座清扫器自找中心.装煤孔盖具有防止倾斜的特点。捣固焦炉导烟孔采用水封结构,密封效果好。
7m
顶装焦炉和6.25m
捣固焦炉的炉门采用弹性刀边,炉门刀边密封靠弹簧顶压,刀边受力均匀,密封效果好。7.63m
焦炉采用的TKEC
型炉门为弹簧门栓、弹性刀边和挠性腹板式结构,刀边弹性力可调节,适应密封面的变形,保证密封严密不漏。
炉顶上升管盖、桥管与阀体承插均采用水封结构,杜绝了上升管盖和桥管承插处的冒烟现象。上升管根部采用铸铁底座,防止了上升管根部因损坏而引起的冒烟冒火。顶装和捣固焦炉按最大孔数配置的基本参数见表1
。
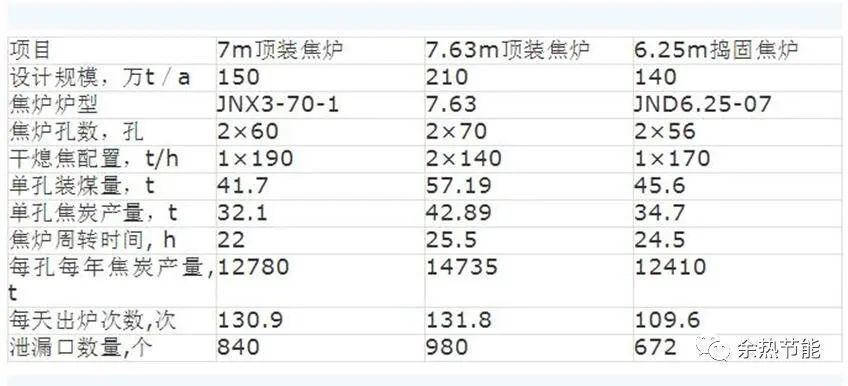
③采用多段加热,减小高向温差,降低火道平均温度,有效降低煤气的燃烧强度。
大容积捣固焦炉的加热系统采用废气循环,降低焦炉烟囱排放废气中NOx
含量。
我国是一个“
富煤、贫油、少气”
的发展中国家,能源消费以煤为主。炼焦工业属于典型的能源流程产业。焦炭生产过程中,煤在焦炉中隔绝空气加热干馏,在生成焦炭的同时产生大量的荒煤气。从炼焦炉炭化室内产生的650~700
℃高温荒煤气,主要成分为氢气、甲烷、芳香烃等,经钢制上升管逸出。为了冷却高温荒煤气,目前世界焦化业传统的方法是喷洒大量70~75
℃的循环氨水,循环氨水蒸发,使荒煤气温度降低,焦油析出,气体进入后序回收工段。荒煤气的净化和热量回收存在大量能源浪费问题,节能潜力和经济效益非常可观。
②焦炉上升管荒煤气带走中高温余热,占焦炉显热总消耗的第二位;

回收红焦显热、上升管荒煤气余热和大烟道烟气余热是炼焦工业节能和余热利用的重点与难点。
煤经高温干馏转化为焦炭,干馏后的焦炭带有大量显热,温度高达1050
℃,熄焦工艺主要有湿法和干法两种。传统熄焦工艺多为湿法熄焦:焦炭在熄焦塔内直接用水喷淋,晾干运至后续工段。高温红焦直接被水浇灭,能量无法回收,产生大量废水和粉尘;由于喷淋水冷却不均匀还会造成焦炭质量不稳定等问题。
目前回收红焦显热主要采用干熄焦技术(CDQ
):高温焦炭从干熄炉顶部装入,130
℃的低温惰性循环气体(多为N2
)鼓入干熄炉冷却段吸收红焦显热,冷却后的焦炭(低于200
℃)从干熄炉底部排出。高温惰性气体进入干熄焦锅炉生产蒸汽,蒸汽可直接并入蒸汽管网或发电。冷却后的惰性气体重新鼓入干熄炉循环使用。具体流程如下图所示。

20
世纪60
年代,前苏联开发的干熄焦技术首先在全世界范围内推广;此后日本对该技术进行了改进,装置更加环保,自动化和大型化。80
年代德国开发了新型干熄焦技术,采用水冷壁式干熄焦设备降低运行成本。
①
增大容积,降低气料比。如莱钢干熄槽的高径比(H/D
)为0.9
,武钢为0.8
,鄂钢小于0.8
;
②
改矩形焦罐为圆形旋转焦罐,避免焦炭偏析,使焦炭分布更均匀;
③
设料钟式分布器和给水预热器,如济钢设置给水预热器后,风料比只有1200m
3/t
;
③
环保,回收1t
红焦显热可减排烟尘0.16kg
、SO21.44kg
、CO20.14t
;
④
干熄焦回收的热能可用于合成氢气和一氧化碳,进而转化为醇醚燃料。

现阶段干熄焦技术发展基本成熟,可充分回收红焦显热并实现节能减排。
在焦炉炭化室内,煤被隔绝空气高温干馏,经过热解生成焦炭和荒煤气。荒煤气温度约为650~750℃,组分十分复杂,按组成性质可划分为水蒸气、净煤气和杂质三部分,具体见下表。

常压下荒煤气中重质焦油冷凝开始温度为400~500℃。此外,荒煤气所带焦油还存在石墨化问题,限制了荒煤气的余热利用。荒煤气余热回收历来是焦化行业的难点,传统工艺采用氨水直接急冷工艺处理从焦炉炭化室逸出的高温荒煤气,造成大量高品质热量浪费。
现阶段荒煤气余热回收技术路线主要有三类,即分布式显热回收方案、利用荒煤气显热将荒煤气制成其他产品和集中式显热回收方案。
这是20世纪70年代我国首创的荒煤气余热利用技术。在上升管周围焊接环型夹套,从夹套下方通入90℃软水与荒煤气换热,换热后汽水混合物被输送至汽包进行气液分离,产生0.4~0.7MPa饱和蒸汽,见下图。

蒸汽送至蒸汽网络,饱和水循环换热。荒煤气换热后温度由650~750℃降至450~500℃。该技术曾在首钢、太钢、马钢等焦化厂使用,投资小、运行成本低,但存在上升管积炭、漏水等现象,且产生蒸汽压力过低。目前这些难题也已基本解决。
该换热器采用高耐热耐腐蚀并经过表面光洁化处理的合金材料,可避免换热器表面焦油冷凝,抑制石墨增长以及上升管堵塞,防止氢腐蚀等优点。与传统上升管换热器相比,该换热器在结构上也有所改进。由内筒、盘管和外壳组成。该结构可有效避免换热介质泄露损害焦炉;换热器内筒与外壳采用承插结构,形成非连续空腔,有效避免了换热器在工作过程中承受的侧向应力,降低了换热器底部出现裂纹的概率,延长换热器使用寿命。并且可产生高温(过热蒸汽)高压蒸汽,并可以取代管式炉。以水为换热介质的荒煤气余热回收方案并未取得突破性进展,仍需进一步完善。
利用导热油(联苯醚)为换热介质,装置结构与水夹套结构类似。高温导热油可为蒸氨工段、煤焦油蒸馏工段和入炉煤干燥工段提供大热量。与上升管换热器相比,导热油换热器采用新型缠绕带式结构。导热油回收荒煤气技术安全性高、操作压力低、换热温度较高。
针对换热器内液体换热介质易泄露问题,莱钢集团赵洪荣提出以空气为介质的荒煤气余热回收方案、杨东伟等提出了以氮气为介质的荒煤气余热回收方案。相比于空气,氮气更加稳定,爆炸风险更低。该方案的余热回收装置与上升管气化技术类似,以上升管为中心,采用螺旋肋片导流的夹套结构以延长换热介质停留时间,具体流程如下图所示。


该装置曾在云南昆钢进行实验,但该实验侧重于荒煤气随结焦周期变化的传热模型,并非以回收荒煤气热量为主。同样该装置对换热器材料以及气密性要求较高。
为充分利用荒煤气所带大量高温显热,20
世纪90
年代德国Dieiner
等提出将从炭化室逸出荒煤气直接裂解,荒煤气中所含焦油、粗苯、氨、萘等经过高温直接裂解成以一氧化碳、氢气为主的合成气,合成气后续可用于合成氨、合成甲醇、生产二甲醚以及直接还原铁等。
该技术可充分利用荒煤气所带大量显热甚至潜热,但是也存以下弊端:
①
将荒煤气中含有的焦油、苯、萘等高附加值化产直接裂解,降低了焦化厂经济效益;
②
直接裂解荒煤气对装置气密性的高要求造成投资成本过高,且存在荒煤气泄露和爆炸风险。
青岛科技大学化工研究所针对荒煤气上升管积炭堵塞等问题,提出了基于洗涤精馏的荒煤气热量回收工艺。直接将重油洗涤、脱除焦油和换热耦合在一个精馏塔内,既能脱除荒煤气中所含焦粉又能达到回收荒煤气余热目的。来自焦炉的荒煤气直接进入精馏塔底部,首先经过具有特殊结构的人字塔盘去除荒煤气中所含绝大多数粉尘,脱除粉尘的荒煤气上升经过塔板与自上而下的焦油换热,彻底除去粉尘。精馏塔设有焦油测线采出装置和换热系统,焦油经过换热冷却后循环回流至精馏塔顶部继续洗涤荒煤气。具体流程如下图所示。

①
利用精馏洗涤塔对荒煤气精馏洗涤,塔内同时实现煤气、重质焦油与高沸点洗油的分离和焦粉的去除;
②
塔中段设有侧线采出,通过侧线采出高沸点洗油在换热器换热产生4.35MPa
的蒸汽。经计算,10km3/h
荒煤气(标准状态下,下同)可产生4.35MPa
的蒸汽为6.3t/h
。
迄今为止,荒煤气显热回收尚未形成成熟、可靠、可规模化生产的工艺,基于洗涤精馏的荒煤气热量回收工艺提供了一种用于解决荒煤气热量回收的新思路。
焦化过程中炭化室所需热量由煤气在燃烧室内燃烧提供,燃烧后产生大量220~300
℃高温烟气直接排入大气。充分回收该部分余热不仅能节能减排,还能产生明显的经济效益和环境效益。
煤调湿(CMC
)技术通过利用烟道气热量加热脱除炼焦煤的部分水分,将水分控制在6%
左右,可降低焦化工段能耗并提高焦炭产量。煤调湿技术发展主要经历第一代导热油煤调湿技术、第二代蒸汽煤调湿技术和第三代烟道气流化床煤调湿技术。现阶段主要采用第三代煤调湿技术,但是该技术需配套庞大的除尘设施;且流化床内易发生设备结壁和堵床现象。针对以上问题,中国某专家团队开发了第四代煤调湿技术,如下图所示。

③
独特的旋转接头技术可避免蒸汽泄漏,减少热损失;
除煤调湿技术外,还可采用热管换热工艺回收烟道气余热:在焦炉总烟道翻板前开孔将高温烟道气采出进入废热回收系统,经装置换热降温后经主烟道排入大气,如下图所示。


该工艺所采用换热器为传统轴向式热管换热设备,具有温度可控、热量输送能力强、无外加辅助动力设备等优点,但是仍存在换热器内积炭现象。
在原有烟道废气余热回收工艺基础上,引入热管蒸发器进一步回收烟道气余热,如下图所示。


烟道气分别经过热管蒸发器、热管省煤器和除氧蒸发器三级换热,热量利用更加充分。热管蒸发器及热管省煤器由若干条热管纵向排列组合置于箱体内,可增大烟气侧传热效率,方便清理集灰结焦,结构紧凑。
1
、 7m
焦炉装煤除尘采用单集气管高压氨水喷射与除尘装煤车及除尘地面站相配合的处理方式,最终排放气体可达到环保要求。
2
、当入炉煤挥发分在(24
±1)
%、水分<10%
时,7.63m
焦炉采用PROven
系统与夏尔克装煤车配合,基本上可实现无烟装煤,效果与喷洒高压氨水加地面除尘站的系统相当,排放气体达到环保要求。
3
、 6.25m
捣固焦炉采用高压氨水喷射装置、双U
形管导烟车、机侧炉门密封装置及炉头烟气抽吸装置,可最大限度地控制烟尘气外逸,环保效果好。
4
、干熄焦技术可回收大部分红焦显热,发展已基本成熟;烟道气热量占焦炉热量消耗比重相对较小,各厂根据自身情况采取不同烟道气余热工艺,但基本达到回收部分余热目的。
5
、近几年国内焦炉上升管荒煤气余热回收利用进入实际应用,
进入快速发展期,
并在长期运行安全性、蒸汽品质和产汽品质指标等方面都有了显著的提高,
为焦化厂焦炉上升管余热回收提供了一种更高效、安全可靠的解决方案。
推荐资料(点击文字跳转):
知识点:大型焦炉的节能减排技术分析