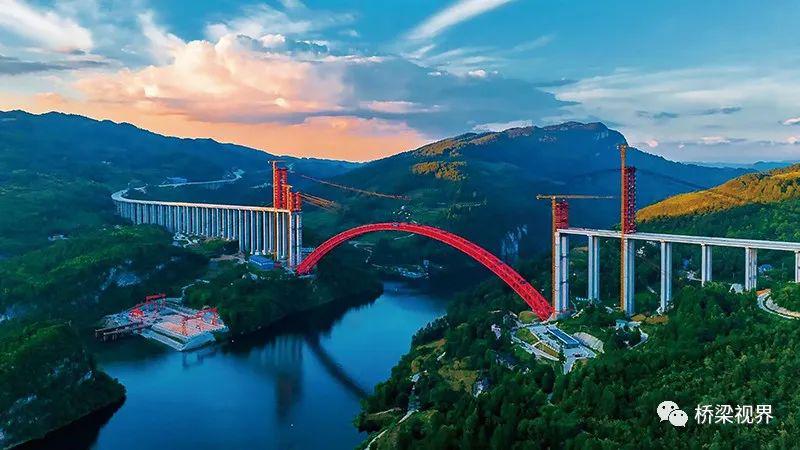
贵州,一个几乎没有平原的地方,最是峡谷纵横、崇山峻岭,也是“盛产”创新桥梁的地方。在碧波荡漾的乌江上空百米,一座橘红色的弧形钢拱,犹如一道绚丽的彩虹,飞跨两岸天险,气势雄伟,这就是乌江特大桥。
乌江特大桥全长1834米,主桥跨度504米,为目前世界最大跨度上承式钢管混凝土拱桥。主拱肋采用8根直径为1.4米钢管组成的等宽变高空间桁架结构,全桥拱肋共有60个这样的节段,最大节段重157吨。同时,大桥首创采用拱、柱、梁全固结无支座整体式受力体系,实行“工厂化制造、标准化生产、模块化安装”装配式建造理念,全桥钢构件均采用高栓连接,大桥栓接精度控制须在3毫米以内,施工极具难度。这座大桥代表了目前同类型桥梁建造的世界顶级水平,也给建设者带来了前所未有的挑战。
绿色“黄金航道”
乌江特大桥主拱钢结构最大节段重量达150多吨,由于大桥横跨乌江,邻近白鹭湖国家湿地公园、石林乌江等景区,出于环保等因素考虑,全桥钢结构在重庆涪陵拼装、焊接、喷漆后,大节段整段运输至施工现场。
大桥位于峡谷腹地,项目团队在现场勘察后发现,现有狭窄、崎岖的山道无法满足如此大节段的运输。倘若新修一条宽阔便道,又会破坏山体自然环境。钢结构运输成为大桥建设的第一个难题。
德余项目总经理代周超在采访中介绍:“利用既有的道路运输如此庞大的钢结构构件,难度非常大,项目团队多次勘察、研究,最终把‘目光’聚焦到乌江这个‘黄金水道’上。”
项目团队先后15次对乌江航道的水位变化、船闸的过闸尺寸、船只的运输能力及船舶运输的程序等情况进行深入调研。从重庆涪陵钢结构加工基地到乌江特大桥建设现场,每艘船舶需穿过4个水电站,单程运输须逆行480公里。由于航道船闸苛刻的尺寸限制,项目团队反复勘察研究,优化设计、施工、钢结构制造方案,最终制定了拱肋1~4节段散件运输再复拼、其余节段整体运输的方案,有效破解了乌江航道跨省市长途运输乌江特大桥主拱钢结构的难题。
乌江特大桥是乌江航道复兴后首次进行桥梁的大型钢结构长途运输。8艘货船40个航次接力运输,7个月的时间“运来”了一座世界级大桥,乌江复航有力支撑了乌江特大桥的建设。
创新“破局之道”
“乌江特大桥首创采用拱、柱、梁全栓接无支座整体式受力体系,栓接安装定位误差要控制在3毫米以内,可谓‘毫米级’精度要求遇上‘百吨级’重量,要实现百米高空中的‘无缝对接’,大桥的建造和精度控制难度为同类型桥梁之最。”德余高速总工肖广生介绍到,“大桥建设伊始,便制定了‘创新驱动、技术先行’总体战略。”为此,项目公司组建了由12位技术专家、4位教授、10余位博士硕士等组成的科技攻关小组,聘请了多名拱桥领域知名专家作为技术顾问,为大桥建设提供宝贵的技术支撑。
历时两年的科技攻关与技术研发,科技攻关小组不断实现理论、技术、装备全方位的创新与突破,为500米级全栓接钢管混凝土拱桥高精度建造奠定了坚实基础。
拱桥成拱理论新突破
乌江特大桥作为世界首座跨度超过500米的上承式钢管混凝土拱桥,首次应用了“大跨拱桥全过程最优控制理论及一次张拉无应力成拱技术”。
“该理论是依托乌江特大桥提出的超大跨度拱桥成拱计算理论。”重庆交通大学副校长周建庭教授介绍到,“乌江特大桥全桥共计240束扣背索,75个索力变量,达到同类桥梁之最,在大悬臂频繁调整索力将面临巨大的结构安全和线形失控风险。项目团队基于‘全过程最优控制理论’开发的索力计算程序,实现了扣背索全过程一次张拉不调索无应力状态成拱,全过程塔偏、应力、索力自动满足结构安全要求,且拆索后成拱线形自动与目标线形吻合。”德余高速项目总工肖广生强调:“在‘全过程最优控制理论’的指导下,大桥的精度控制重心被转移到拱肋厂内制造阶段,大幅降低了主拱肋吊装阶段的精度控制难度。”
全栓接精度控制技术创新
全栓接拱桥卧拼+立拼双拼施工技术
“大跨径钢管拱桥主拱、立柱、主梁全栓接设计是在国际上首次采用,在面临无同类型项目借鉴及无相关规范标准指导的条件下,项目提出‘卧拼+立拼双拼施工技术’,有效解决了全栓接设计毫米级制造精度要求。”钢结构加工单位中交世通重工有限公司总工张慧丽介绍,“双拼施工技术是基于设计、监控、安装等各参建方的控制标准及要求,摸索、总结形成了36道标准施工程序、22项工序报验、17项关键控制指标,相关成果对完善相关规范和项目推广应用提供了技术支撑。”

三维激光扫描数字化预拼装技术
代周超在采访中介绍到:“乌江特大桥采用了‘工厂化制造、装配式建造’的设计理念,装配式建造是未来施工技术的主要发展方向。钢结构厂内的双拼施工及拱肋吊装施工是一个‘搭积木’的过程,但是桥梁的构件重达百余吨,周转、吊装、调整一次需要大量的场地、设备机具、劳动力和时间投入。在工期、成本、精度、质量多重压力下,项目团队不得不寻求新的技术方案,项目组最终聚焦到‘数字化预拼’这一前沿技术。”
项目团队依托“山区桥梁及隧道国家重点实验”开展了三维激光扫描数字化预拼装技术专项研究,解决了大型桥梁构件精度优于2毫米的模型重构、数字空间模型三维姿态自由调整、吊装姿态与变形预测等关键问题。
“数字化预拼装技术在装配式结构的制造、安装技术中展现出巨大的潜力,”钢结构加工项目总工郑永介绍到,“在拱肋立拼阶段,数字化预拼装技术可以自动预测拱肋节段的胎架线形,使拱肋立拼线形自动与设计线形高精度吻合。仅每一轮次立拼的拱肋线形调整一项,数字化预拼装技术便节省4天时间和大量的人力、机具投入,为乌江特大桥顺利合龙抢占了制胜的时间节点。”数字化预拼技术是目前装配式建造中最为前沿的研究热点之一,在大型钢结构桥梁中大规模应用数字化预拼装技术,乌江特大桥属世界首次。

栓接结构安装控制方法与姿态精调技术
2022年1月乌江特大桥南岸首节段吊装到桥位,采用传统方法历时20余天的调整始终难以达到栓接精度控制要求。对于常规的拱桥,将拱肋上的监控测点调整达到理论目标位置时,即可代表拱肋线形调整完毕,该方法却在乌江桥的首节段调整中“失灵”了。
在进度与数次姿态调整失败的双重压力下,项目团队曾一度要放弃首节段的安装精度。乌江特大桥项目经理王志金回忆道:“乌江特大桥主拱拱肋、横撑、腹杆均采用高栓连接,首节段是大桥的‘基础’,若无法实现首节段螺栓的顺利安装,主拱9万个螺孔将全部无法安装,我们没有后路可退。”在项目团队最黑暗的时候,传来了立拼厂内三维扫描数字化预拼装技术应用成功的捷报,项目团队看到了新的曙光。
项目团队使用扫描模型一次次复盘、推演,在三维数字空间中,终于“看见”了栓接结构安装控制的核心。随后,一种全新的栓接结构安装控制方法——“原形复位法”被提出,该方法的主要原理是在制造阶段采用三维激光扫描技术精准记录制造阶段各个构件之间的相对关系,然后在安装时严格复原制造阶段的三维姿态相对关系,实现所有栓接孔的精准对齐。
“安装目标有了,但拱肋的调整可谓‘牵一发而动全身’,要使一个百余吨的庞然大物的三维姿态精准达到目标,‘凭感觉’是行不通的,”乌江特大桥项目总工陈诗泉说道,“应用三维扫描技术,可以快速分析实际拱肋三维姿态与目标的偏差,并自动给出三维姿态调整顺序和调整量,利用测量机器人实时监测、反馈控制拱肋的调整过程,这就是我们项目研发的三维姿态精调技术!”随着原形复位安装控制方法及三维姿态精调技术的应用,左右幅两个首节段仅用时3天便完成了拱肋的精调和栓接,为主拱高精度成拱奠定了坚实的基础。

装备创新 提质增效
为了满足新理论、新技术、新方法的落地应用,项目团队同步研发了系列新型装置、装备。
在首节段精调方面,设计了多点约束支架与三维千斤顶组合精调装备,使毫米级安装目标精度得以实现。在斜拉扣挂索力预紧与张拉方面,研发了快速自动连续预紧、等应力智能张拉设备,以满足项目全过程索力一次张拉不调索的精度控制要求。在大型构件高空安装与精细化调整方面,研发了高空安装精调吊具,实现构件的纵向姿态、横向姿态、旋转姿态的精准调整,提升构件高空安装精度和效率。


“面对乌江特大桥这样极具挑战而又无经验可循的项目,‘创新驱动、技术引领’才是大桥建设的‘破局之道’!”肖广生总结道。
数智铸就世界桥梁
“数智化建造,铸就世界桥梁。”这是项目进场伊始确立的大桥建设思路。数字化、智能化技术的全面应用是乌江特大桥高质量、高标准、高精度建造的排头兵,大桥在数、智技术多个方面的应用达到了行业先进水平。
智能云监测全面应用
针对乌江特大桥这一世界最大跨度的上承式钢管混凝土拱桥,项目团队研发了拱桥斜拉扣挂缆索吊装全天候智能云监测系统。全桥设置700多个传感器,犹如听诊器24小时监测着每一丝“脉动”;全套智能监控系统和北斗定位系统,让缆塔偏位、缆塔应力、缆索索力、锚碇滑移和拱肋吊装参数全数据化;徕卡TS60全自动测量机器人全面应用,相关监测成果揭示了该类型桥梁的线形变化规律,为拱肋的高精度安装、定位提供了极其重要的数据支撑。
数字化建造全面应用
在拱肋制造线形数字化检验、“N+1”预拼线形精准接续、拱肋安装三维姿态精测精调、拱肋精准封铰、拱肋大悬臂三维线形快速精测、拱肋合龙三维最优姿态预测等方面全面应用数字化预拼技术,数十亿个扫描点全覆盖,“X光”全身深度检查,对结构件制造线形与安装姿态了如指掌。三维互动交底、全息投影、AR及滑轨屏等可视化技术直观呈现每一道施工工艺。BIM+GIS技术对大桥场地精细化设计及工艺模拟,实现大临方案合理、成本可控。360°视频对重点施工部位、风险管控点实现全方位监控,提升项目现场监管水平。
数字化管理全面应用
桥拱肋各项工序实行质量实名制管理制度,通过二维码扫描方式填写关键内容,压实作业人员和技术管理人员责任,提高工程整体质量。特种设备采取线上监控+线下检查的组合方式,拱肋节段吊装前,按照分工对各系统进行安全检查,将数据上传至平台,后台分析整理汇总,提高设备管理效率。

高精度合龙 大桥虹臂“成功牵手”
凌晨两点的乌江河畔,乌江特大桥智能云监控中心热闹非凡,大桥拱肋上黑夜如同白昼被四周灯光照亮。
“全桥温度准确达到预设合龙25℃,开始张拉北岸左幅15号扣背索至100%!”项目负责人现场指挥道。控制中心下达拱肋合龙线形精调指令,扣背索同步张拉一气呵成。凌晨三点,4台全天候监测测量机器人及高精度三维激光扫描完成全拱三维线形测量。
“乌江特大桥南岸合龙定位误差1.5mm!北岸合龙定位误差1.2mm!8根弦杆合龙对准偏差全部小于3mm!”“温度25℃稳定!风速1.3m/s,风速稳定!”各项喜人数据从四面八方汇入控制中心,大桥监控单位逐一确认各项参数,当即下达合龙指令:“乌江特大桥精准达到合龙姿态,开始锁定!”随着合龙段最后一颗高栓施拧完成,大桥虹臂“成功牵手”,实现高精度瞬时锁定。

主拱合龙只是乌江特大桥众多“关卡”中的一道,建设者们将继续迎接管内C70混凝土灌注、拱上立柱安装、桥面梁安装、UHPC桥面板安装等一项项重大挑战。
乌江特大桥结构体系设计新颖、建造理念前沿,该桥的建设,对于促进拱桥设计理论发展、拱桥快速建造技术革新等方面具有重大意义。而以“创新驱动、技术引领”作为指导方针、校企共建联合研发团队的模式,是“全过程最优新理论”“数字化预拼装技术”等前沿研究能够落地、服务于工程的关键。乌江特大桥即将迎来全栓拱上结构安装。届时,项目团队将面对的是桥梁建造的最高控制精度。现在已经启动了拱上结构百米高空毫米级精度建造的技术攻关,并且已经在理论上突破了核心技术瓶颈,项目团队对该桥的如期建成充满信心!

大桥建成后,将连接贯通贵州省高速公路网中南北走向沿河至榕江的高速公路,并与周边国省道、县乡道、通村公路构成完善的交通网络,紧密联系重庆、沿河、德江、思南、凤冈、石阡、余庆、黄平、凯里、榕江及沿线乡镇等重要经济节点,极大地带动沿线的资源开发利用,促进该地区经济发展和少数民族脱贫致富,可以说是一个实实在在的民生项目。大桥通车后,将进一步提高区域交通通行能力和服务水平,对推进贵州交通强国西部示范省建设,促进沿线产业结构升级、资源开发利用、旅游产业发展具有重要意义。